Internet of Things ( IoT)
How can the Industrial Internet of Things (IIoT) & Digitalization revolutionize manufacturing plants?
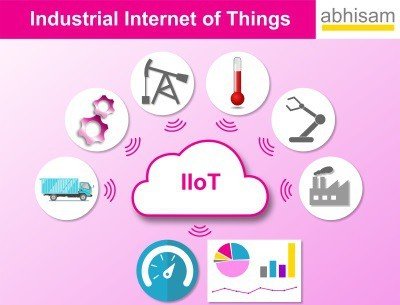
Executive Summary
The Internet of Things (IoT) for short has become a buzzword used extensively and it is also currently very high on the Gartner Hype Cycle. There is a lot of chatter in the media about smart health bands, or refrigerators that order online when they sense empty shelves. Although these are far from becoming reality due to several practical issues, do not dismiss IoT technology as also being just hype. It has the capability to completely revolutionize manufacturing as we know it today. Not just discrete parts manufacturing, but also large process industries can benefit tremendously from IIoT technology. This Abhisam white paper shows how you can start using it in your industrial applications. Abhisam has several RFID and IoT training courses and workshops, webinars that you can participate in.
This white paper shows how you can start using it in your industrial applications.
Introduction
The IoT word was coined by Professor Dr Sanjay Sarma, from MIT, when he was working on RFID Technology. This was something like about 15 years ago. At that time RFID technology was slowly replacing bar codes in the supply chain. Dr Sarma thought that we should not just automatically identify packages, containers and other “things” that moved in global supply chains at just a few choke points like at warehouses or shipping docks, but we should also track them via the internet, as they moved from factory to warehouse to ship to trucks to stores. He called this concept, the Internet of Things and this moniker stuck. Over the next few years, the concept then became bigger and more better because it started adding other things such as sensors, transmitters, controllers, displays and other things to it, it was not now just restricted to RFID tags. Meanwhile the management consultants started hyping it up as a possible game changer for any kind of business. This got picked up by the business press. Rapidly it started becoming part of the discourse in the seminar circuit and before you knew it, industry leaders started publicly talking about it.
Meanwhile, as Moore’s law still applied and as microprocessors and microcontrollers became smaller, faster, more robust and cheaper, it became very attractive to use them in factories where hitherto there was very little of instrumentation or automation.
Industrie 4.0
If we study history, we find that in human history, industrialization moved through certain distinct phases, starting by using animals to do menial work such as ploughing fields, to using steam & electricity to power machines, next by using computers to control them and now where we are in the fourth phase of the industrial revolution. In this phase we will have ubiquitous computing and connectivity, autonomous machines and the like, having little human intervention. This fourth industrial revolution is known as Industrie 4.0 (German term). There is some ambiguity about what part is Industrie 4.0, what part of Industrie 4.0 is IIoT and how they will work together. However, for now just remember that the IIoT will be a big part of how Industrie 4.0 is implemented.
(White Paper continues below….)
Different Automation Architectures
If you have been in industry for long, you will have realized by now that different industrial sectors have different automation architectures, which can be divided into two main types, one is prevalent in discrete parts manufacturing and the other in the process industries. This new technology surprisingly, benefits both kinds of architectures.
What is the situation in Discrete Parts Manufacturing?
In our view, Industrie 4.0 was a term that was more applicable to discrete parts manufacturing that uses standalone machine, such as for example an auto parts maker or a plastic mold maker or a nut and bolt maker. The raw material goes though certain distinct stages, each stage having one or more machines in a work cell or work center. Most of the work centers are only connected via assembly line kind of conveying systems. So in such a discrete parts manufacturing factory that makes widgets, one may have different machines such as drilling machines, lathes, conveying systems, packaging and so on. Every machine and/or work center may have different automation systems, depending on the complexity and whether they have been sourced from one maker or many. They may also have different levels of automation for example, a simpler machine may have no programming capability, only a few relays and on/off buttons whereas another one may be CNC (Computer Numeric Control) type or even a PLC (Programmable Logic Controller) type with local display panels having graphics. All of them, may or may not be connected to a higher level system such as an MES (Manufacturing Execution System).
How does IIoT improve the discrete parts manufacturing plant?
Using the Industrial Internet of Things enables the plant owner or manager to get a single big picture view of the plant, that is created by utilizing various kinds of sensors/transmitters and edge devices to capture data from individual machines. This data gathering and analysis can throw up new opportunities for improving the Operational Efficiency & Overall Equipment Effectiveness (OEE) of the entire facility.
We can measure parameters that traditionally were never measured, such as the operator presence on the machine, operator actions in a shift, lube oil temperature variations during the shift and so on. This data pool can then be run through analytical programs to find room for improvements.
This entire process is also referred to as Digitalization.
What is the situation in the Process Industries (Chemical, Oil & Gas, etc)?
On the other hand if we see any process plant (such as a chemical manufacturing plant) it may typically have one or several units and they may have various sensors, transmitters, control valves, on off valves- all of which are operated by a DCS (Distributed Control System) or a PLC-SCADA(PLC coupled with a Supervisory Control and Data Acquisition) system. These systems have been controlling plants in this fashion for several decades now.
In the last few years there have been inroads of Fieldbus technology, but not all new plants have embraced it. There were several competing fieldbuses and amongst them FOUNDATION Fieldbus seems to be the most popular in the process industries, Profibus DP in the non process industries and ASi bus in smaller machines or skid mounted units. However they are all different protocols, have different physical layer specifications and different message structures. MODBUS is an even older protocol, but it primarily used in controller to controller communication, rather than field instrument to controllers. For field instruments like transmitters (flow, level, pressure, temp of different types) and valve positioners, FOUNDATION Fieldbus still remains the most popular.
Digitalization can have huge paybacks in this situation because we can now measure many more parameters and study their relationships to derive insights.
What is the present state of Hybrid plants?
Many plants have both kind of manufacturing processes. This is the case with plants that make pharmaceuticals or beverages or pesticides. For example a beverage plant may consist of a process plant where the bulk liquid is manufactured (think reactors, distillation columns, filters, etc) and then a downstream formulation plant where one has more “machine automation” kind of setup where the bulk ingredients are mixed with other ones, then filled in bottles and packed, shrink wrapped and boxed into cartons. Also some process plants have smaller sub units that are distinct from the main plant. These could be utilities such as Boilers, Cooling Towers or Nitrogen generating plants. They could also be large compressors or captive power plants using gas turbines. These skid mounted plants come as a package unit with their own PLC and HMI. This is not completely integrated into the main DCS, although connections via some buses such as Modbus are provided to get some key parameters.
Common Problems
In all the above examples, the present design results into various “islands of automation” amongst a large set of semi-automatic and manual operations. The reasons may be design based (many EPC contractors have this kind of design philosophy for various reasons that are not technical) or they may be historical, such as the plants may have been built at the same site but at different points of time. For example, a petrochemical unit may have started out with one single liquid product. Let us call it A1 in one plant, with one DCS. A1 is sold to customers in bulk via tank trucks. Then, after 5 years, the management added another plant for another product A2 (also liquid), with another (latest and greatest state of the art DCS with a different technology). This was also sold to customers in drums and the drum filling system was controlled by a PLC. Still 5 years later they decided to add another plant with a new product A3 that was a reaction product of A1 and A2 called A3, which is a solid and is sold in bags with several bagging machines being part of the plant. The bagging machines are also PLC controlled, with perhaps a robot packing them in cartons and shrink wrapping them. So now in the space of about 10-15 years the factory has at least two different DCS, three different PLCs and a stand alone robot. If the utilities such as boiler, cooling tower and Nitrogen plants have their own PLC systems then actually the plant has six different PLC systems.
No way is the site manager going to have a single picture view of the plant!
What is different in IIoT?
Do not believe consultants who tell you that IoT is only for “operational information” whatever that may mean. IIoT is capable of completely replacing whatever was being done by PLC-SCADA and DCS systems. If you are aware of the so called “automation hierarchy”, it had (still has) several layers of devices and systems. On the bottom are the so called field devices (sensors, transmitters, switches, valve actuators, etc) then you have the controllers housed in marshalling panels and then these are connected to the DCS which is then again connected to the MES or ERP systems and so on. IIoT promises to flatten the structure. Arrival of robust, powerful, small footprint and CHEAP controllers means that your lowest level devices can act as smart ones. They can then connect to your IIoT Platform by a variety of ways, which are also many times more SECURE than the current industrial protocols. Your operators and managers can view the plant information from the same platform on any device including handhelds. This is eerily similar to how middle managers are no longer needed in many organizations , since they flattened the management structures.
Open interconnect standards mean that you are not locked into any particular automation vendor. So not only your capital cost, but also your entire lifecycle cost can be brought down dramatically whilst on the other hand you have huge sets of information that can be analysed and interpreted by many techniques (Big Data, Machine Learning, AI, etc) to have more insights and squeeze that extra dollar from your operations, adding to the bottomline.
Outside the plant
Digitalization can yield benefits not just for the plant, but for its entire ecosystem. A plant is not alone in the economy. It has raw material suppliers (who may be other plants) and customers (who may be other plants, not necessarily consumers). The supply chain for this system depends on transporters and warehouse operators. More value can be derived by IIoTing (or Digitalizing) the entire supply chain, not just the plants. For example, do you see tank trucks waiting at your materials gate to deliver stuff but you cannot unload it because your raw material storage tanks are full? And do YOUR own trucks wait outside your customers gates because THEIR tanks are full? Do you keep excess inventory because you are not sure if you have to shutdown your plant because you have no idea if the material you ordered is delayed in between?
All these problems can be solved.
Sounds Interesting?
Get in touch with us to know how to implement this in your own factory, plant or organization.
IIoT related Training Courses and Webinars
Attend this free online IoT workshop to learn more about the Industrial Internet of Things and Digitalization.
Learn from practising engineers & not academics.
Take this popular RFID Technology training course to learn Radio Frequency Identification in detail and qualify as a RFID Professional. Covers everything in detail with extensive animations, simulations and example case studies.
Contact Us by filling the form below OR call us OR email